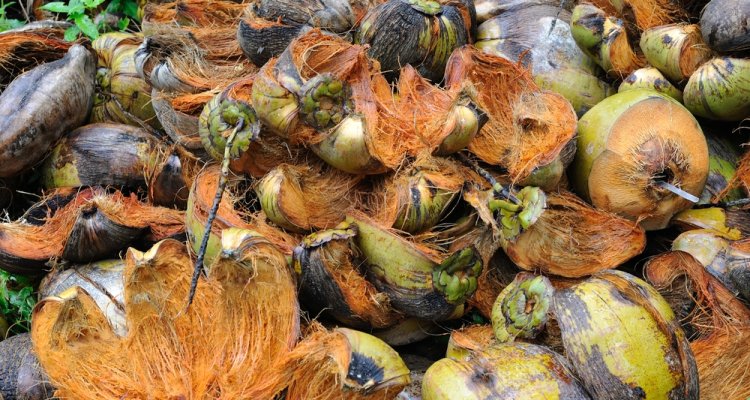
Project
Construction material from coconut waste
In tropical countries, coconuts are used for their pulp and milk.
Traditionally, products such as coconut mats and brushes are made from the husk, the hard, hairy shell. Because the husk contains a lot of lignin which acts as a natural adhesive, the department of Biobased Products at Wageningen UR discovered that sustainable production of board material from the husk was also possible.
Biobased Products at Wageningen UR has developed a method to manufacture high-grade board material from the husks of coconuts. The procedure for making boards is already old. However, the difference compared with existing production methods is that the husk is processed in a 100 per cent natural way into smooth boards or other forms. This process does not require the addition of glue or chemical binders. The technology to produce board material from coconut waste was developed in conjunction with institutes in the Philippines.
Coconut fibres
The husk of a coconut comprises 30 per cent coconut fibres and 70 per cent flesh. Those are separated from one another, after which traditional products, such as mats and brushes, are made from the fibres. The flesh contains a significant amount of lignin, a substance that is found in ligneous cell walls. In a melted form, that is suitable as an adhesive for the coconut fibres.The husk of the coconut is separated for the production of boards. The husk is processed into small pieces and pressed under hot pressure into boards. As regards its properties, such as sturdiness and fire safety, the board material (called ecoco boards) that is obtained is comparable to or better than medium density fibreboard (MDF).
Sustainable and environmentally friendly
The use of coconut husks for the production of board material has a number of advantages:- The method is sustainable and environmentally friendly. The residual material of the coconut is used in its entirety. It is a good alternative to wood and helps to prevent deforestation. During production, glue and chemical agents do not need to be added. Furthermore, the production is CO2 neutral.
- It is inexpensive. The glue that has to be added when boards based on wood fibre are made contributes to one third of the total production costs. Glue is not required to process coconut husk into board material.
- It can form an extra source of income for farmers in developing countries.
Coconut-producing countries
The board material that is made from coconut husk can be used for all kinds of applications, for example, in the construction sector, such as wallboards, frames and similar. The material is intended for both local consumers and for export, for example, the furniture industry. The study is funded by the Common Fund for Commodities (CFC), a collaborative project between 100 countries that supports and assists agricultural projects.
Biobased Products is currently considering the options for large-scale production. A production factory is being set up to this end. The intention is to transfer knowledge and technology to coconut-producing countries, such as Sri Lanka, India, the Philippines and Indonesia.
Links:
- ScienceDirect: Binderless boards from whole coconut husk
- Common Fund for Commodities(CFC)
- United Nations Food and Agriculture Organisation (FAO)